What is the main production schedule of MPS?
Why should every company pay special attention to the main production schedule of MPS? Planning is one of the most crucial aspects of any task. Additionally, a significant part of work in the production process is production planning. The production planning process contributes to reducing production time and costs. Through precise planning and scheduling, accurate predictions of product manufacturing within specific time intervals can be achieved.
In this article, we will first discuss the main production schedule of MPS, the primary applications of the main production schedule of MPS, different components of the main production schedule (MPS), and the advantages of utilizing MPS. Then, an example of MPS utilization in a leather factory will be described.
What is the main production schedule of MPS?
When we plan to produce all products individually in short time intervals, the planning becomes more precise. In this type of planning, apart from the main product groups, each product is examined separately, and we create a plan for producing them.
This kind of planning is usually carried out on a weekly basis, and the output it provides us is referred to as the main production schedule. This way, we exactly know how many units of each of our products we will produce in each week.
Therefore, in a production unit, through the main production schedule of MPS, the quantity and timing of product manufacturing are determined over a specific period. In other words, the main production schedule defines what type of product, at what time, and in what quantity will be produced.
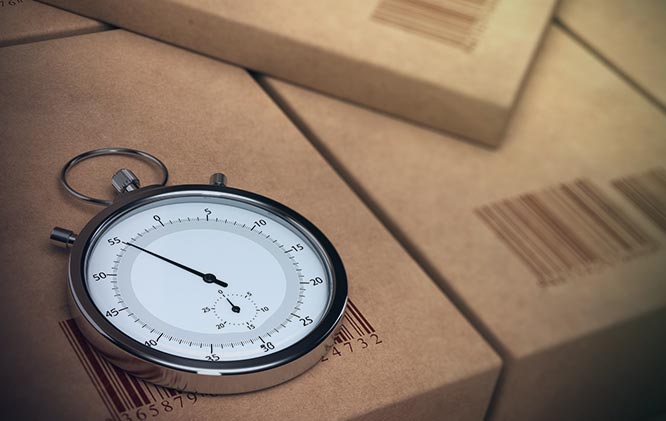
The main production schedule determines the quantity and timing of product manufacturing throughout a period.
The required product quantity for production usually consists of two parts as follows:
- 1. The amount of the product determined through orders received from customers.
- 2. The quantity of uncertain demand obtained through statistical forecasts.
In general, the main production schedule of MPS is an overarching plan for assessing the production of final goods in a manufacturing unit. When executed correctly, the main production schedule of MPS yields several results, including:
– Making necessary adjustments in the case of demand fluctuations.
– Enhancing the efficiency of the production unit.
– Effective cost control.
Primary Applications of the main production schedule of MPS
The main goal of the main production schedule of MPS is time-saving. As a result, the time spent on production management becomes more efficient, ultimately leading to the expansion of the manufacturing business. The other objectives of the main production schedule all align with achieving this goal. Before delving into the applications of production scheduling, if you are not familiar with production management, be sure to read the production management article.
Translation of Production Planning
With the assistance of the main production schedule of MPS, the quantity of production in a specific period is determined. This leads to proper management to create a balance among demand, workforce needs, and equipment capabilities.
Evaluation of Alternative Plans
Through the use of the main production schedule of MPS, different production methods are examined, and errors and issues in the production line are identified, ultimately selecting the most efficient production method.
The process of planning, directing, controlling, and organizing ongoing activities in a production unit to transform input resources into products is referred to as production management.
Production of the required capacity
Through the main production schedule of MPS, it becomes feasible to achieve the actual capacity needed to meet demand, increase profits, and minimize unit production costs.
Facilitating Information Processing
Using the main production schedule (MPS) and generating a timeline, reorder points for delivering goods to customers are set. This is achievable through the coordination between various management information systems such as marketing, finance, etc.
Demand Management and Supply
MPS helps companies predict customer demands more accurately and plan production in alignment with those demands. This ensures timely production and delivery of products to customers.
Resource Efficiency
With the main production schedule in place, raw materials, workforce, and equipment are allocated with greater efficiency. This leads to increased production efficiency and reduced resource wastage.
Cost Reduction
Through more logical production sequencing and optimized inventory management, production and inventory costs are reduced.
Responsive to Demand
MPS allows companies to accurately and promptly respond to customer demands, facilitating customer acquisition and retention.
Supply Chain Management
Using MPS, companies can establish better coordination in the supply chain, provide better information to stakeholders, and engage in more effective interactions with suppliers.
Reducing Sudden Changes
The main production schedule reduces the need for sudden changes in production and inventory management, enabling better adaptation to market changes for companies.
Improving Production Quality
By proper production sequencing and precise inventory management, the likelihood of producing low-quality products is reduced, leading to an improvement in production quality.
Which Industries Use the Main Production Schedule (MPS)?
In general, the main production schedule of MPS is utilized as a powerful tool for improving the order and coordination of processes and resources in any given industry. It is used to help industries achieve goals of efficiency, quality, and responsiveness to demand. In fact, the main production schedule (MPS) is not only employed in manufacturing companies but also across various industries and even service organizations. This method is employed to enhance planning and resource management to achieve production objectives, high efficiency, and responsiveness to demand. Some of the industries that utilize the main production schedule of MPS include:
Service Industries: In service sectors like transportation, postal services, technical services, and maintenance, the main production schedule helps managers optimize resource utilization and task allocation. For example, in transportation, routes and vehicle scheduling can be optimized using this method.
Healthcare Industries: In healthcare facilities, the main production schedule assists managers in optimizing patient appointments, scheduling, physician tasks, and medical staff arrangements. This can aid in responding to patient demands and improving service quality.
Financial Industries: In the financial and banking sectors, the main production schedule is used to manage workflow and process financial transactions. Improved scheduling can lead to reduced conflicts and enhanced accuracy in transaction processing.
Education and Research Industries: In universities and educational centers, the main production schedule is used to organize teaching programs, courses, allocated time for research projects, and other academic tasks.
Customer Service Industries: In customer-centric industries such as mobile or communication services, the main production schedule helps managers improve response times to customers and allocate resources for resolving customer issues.
Utilizing the Capacity of the main production schedule of MPS
Ultimately, the main production schedule of MPS determines the requirements for using machinery and equipment.
The additional objectives of the main production schedule of MPS are as follows:
- It leads to improving demand conditions.
- It reduces delivery lead times.
- It promotes standardization of communications in business.
- It aids in prioritizing needs.
- It contributes to maintaining stability in production.
- It creates executable plans for production orders.
Different Components of the main production schedule of MPS
The various components of the main production schedule of MPS include demand management, production planning, inadequate capacity planning, the main MPS itself, and materials planning. These components are illustrated in the image below.
To establish and organize a production calendar, a demand plan is required. Developing a demand plan necessitates accurate sales time information. This information is used to forecast and estimate demand for the upcoming week. The plan should be structured on a weekly basis.
Additionally, the creation of inventory reserves can be an effective strategy for handling unusual or high-volume orders. If demand increases, the order plan should be adjusted to prevent excessive stockpiling.
Consequently, each week, the demand plan is updated to create an accurate production calendar. This process is dependent on the main production schedule (MPS) plan.
A production unit must meticulously fine-tune the main production schedule of MPS and utilize it as a valuable tool for fulfilling business orders. The correct steps for creating a main production schedule (MPS) are as follows:
- Preparing and configuring a product checklist.
- Preparing and configuring sub-checklists for each product.
- Performing annual, monthly, and weekly planning.
- Planning for weekly production quantities.
Advantages of Using MPS
Considering that the main production schedule of MPS serves as a tool for demand forecasting, it brings numerous benefits to an organization. The most important advantages are outlined below:
- Improved Demand Planning: A better understanding of production cycles leads to more efficient and optimized demand planning.
- Ideal Inventory Levels: By examining production requirements, the optimal inventory level is determined.
- Human Resource Allocation: The production unit’s human resources department can be aware of the necessary requirements for production before actual production takes place.
- Material Capacity Optimization: The required material capacity can be optimized, preventing material stockpiling.
- Maintenance and Repairs: Being aware of the ongoing production volume allows for feasible maintenance and repairs on the production line.
- Estimated Workforce: The required workforce for future productions can be estimated.
- Enhanced Purchasing: MPS allows for the calculation of required materials for future production, leading to improved purchasing processes.
- Financial Projection: The financial department of the production unit can predict a suitable cash flow for the unit with the help of the main production schedule.
By utilizing the main production schedule of MPS, organizations can benefit from streamlined operations, better resource allocation, reduced wastage, and improved overall efficiency.
Effective Approaches for Main Production Scheduling
In general, main production scheduling (MPS) is recognized as a key factor in improving productivity and efficiency in the production process. Selecting appropriate methods for MPS depends on the characteristics and needs of your organization. Additionally, combining multiple methods can contribute to overall scheduling and production performance enhancement. Below, we highlight some effective approaches for creating a main production schedule:
Process Analysis: Initially, it’s essential to thoroughly analyze the entire production process. This analysis helps identify production stages accurately and select the best sequence for them.
Identifying Weak Points: Identifying weaknesses and delays in the production process can lead to significant improvements. Combining these weak points can result in an efficient schedule for the main production.
Use of Scheduling Software: Utilizing project management and scheduling software can simplify and enhance the accuracy of the scheduling process. These tools allow you to arrange production stages in your preferred order and create a more precise schedule.
Implementing Smart Production Methods: Techniques and methodologies like Lean workflow and Agile production can help optimize and streamline the production process.
Simulation Utilization: Simulation can help identify weaknesses and issues in the main schedule, allowing for necessary adjustments to improve the process.
Learning from Past Experiences: Previous experiences in manufacturing and scheduling can guide you in choosing the best methods. Learn from past mistakes and leverage successes.
Human Resource Management: Allocating suitable human resources with the necessary skills for controlling production stages and scheduling can have a significant impact on productivity.
Setting Priorities: Set priorities based on the importance and urgency of production stages to achieve the best production scheduling.
Continuous Monitoring and Updating: The main scheduling process is dynamic. Keep updates and changes aligned with shifts in the business environment and processes.
Team Collaboration: Production teams and managers should collaboratively determine the main production schedule and implement necessary changes actively.
By implementing these effective approaches, your organization can benefit from optimized production scheduling, increased productivity, and improved overall efficiency.
How to Schedule Production Processes Using Master Production Scheduling?
Producing a product relies on organizing and sequencing processes accurately. This is where the Master Production Schedule (MPS) serves as an efficient tool to help align and optimize these processes. In general, aligning processes with the master production schedule requires a precise approach, team coordination, and continuous updates. In this section, we provide tips and strategies for aligning processes using the master production schedule. By adhering to the following points, you can enhance production performance and increase efficiency.
Identifying Production Stages:
First and foremost, you need to identify all the distinct stages of the product manufacturing process. From the entry of raw materials to the delivery of the final product, each stage should be carefully pinpointed.
Assessing Time Requirements for Each Stage:
Thoroughly examine the amount of time needed for each production stage. This estimation allows you to focus on a more precise execution sequence of production stages.
Setting Priorities:
Identifying fundamental and critical production stages that require prioritization is highly crucial. Processes influencing the delivery and quality of the final product should take precedence.
Logical Sequencing of Stages:
Utilize the master production schedule to logically sequence production stages. This arrangement should lead to reduced interferences between stages and an overall improvement in production performance.
Resource Allocation:
Based on the master production schedule, determine the resources required for each stage. These resources encompass human labor, financial resources, and materials needed for each stage.
Consistency in Adjustments:
The master production schedule should be regularly updated and synchronized with changes in the business environment. Consider that conducting regular updates is a strength of your scheduling.
Utilizing Project Management Tools:
Utilizing project management software and tools aids in refining and monitoring the master production schedule. These tools provide more precise insights into the order and status of process stages.
Team Participation:
When aligning processes with the master production schedule, various teams must engage actively in this process. The experiences and insights of team members can contribute to enhancing the scheduling.
Continuous Management:
The master production schedule should undergo continuous management. Periodic evaluations and updates based on market changes and business environment contribute to better process alignment.
Enhancing Productivity and Optimization:
By applying a more precise order and alignment to processes, productivity increases, and the potential for optimizing overall production performance emerges.
Sample Use of MPS in a Leather Factory
A sample Master Production Schedule (MPS) for a leather handbag manufacturer is provided below. Note that for the sake of clarity and simplicity in this example, a production facility with two products, each having two variations, totaling four Stock Keeping Units (SKUs), is considered.
- The initial product inventory level is recorded.
- The forecasted demand is added below the inventory level.
- Ultimately, the production quantity is calculated based on the inventory level, demand, and current capacity.
It should be mentioned that SKU stands for Stock Keeping Unit, representing a unique inventory item. An SKU for a product can consist of one or more numbers and letters, or a combination of both. In other words, an SKU serves as a distinctive identifier for manufactured products. Its purpose is to differentiate one product from another within a manufacturing unit.
The above example is one of thousands of Master Production Schedule (MPS) schedules used in various businesses. The lack of flexibility in the plan and its inability to adapt to actual production orders and capacity constraints are among the negative aspects and drawbacks of the plan. Additionally, due to its use of Excel for design and data entry, it requires manual updates by the user. For this reason, manufacturers aim to implement dynamic and appealing MPS schedules using Manufacturing Execution Systems (MES) software. However, if you are considering acquiring a production scheduling system, it’s advisable to familiarize yourself with software purchasing tips before making a decision.
In addition to modern management systems, Manufacturing Execution Systems (MES) are utilized for data recording, operational control, and swift responses to system outputs. These systems are based on defined functions to provide real-time monitoring and immediate intervention on the production line. This enables the identification and halt of potential errors during production, ensuring efficient management alongside rapid problem-solving.
Example of Using MPS in a Manufacturing Company
Imagine a manufacturing company that produces a variety of electronic products, including mobile phones, televisions, and laptops. During a period of increased product diversity and customer demand, the company faces challenges in production sequencing, inventory management, and supply chain coordination.
To address these challenges and enhance the efficiency of production processes, the company decides to leverage MPS technology as an effective tool. Initially, accurate information about inventories, demand, and production capacity is input into the MPS system. This information is stored in the system’s database.
Subsequently, using optimization algorithms, the MPS system generates a production schedule in an appropriate order and configuration. This scheduling includes determining the sequence of producing products, the quantity of production in each time period, and optimal resource allocation for each product.
By utilizing MPS, a company can achieve the following objectives:
- Better Inventory Management: With accurate inventory adjustments and production sequencing based on demand, inventory levels are minimized and costs are reduced.
- Enhanced Supply Chain Coordination: Aligning production sequencing with demand increases coordination between production stages and the supply chain, reducing delays.
- Improved Efficiency: Optimizing production sequencing leads to increased efficiency of production machinery and equipment.
- Responsiveness to Demand: By sequencing production based on demand, a company can better respond to customer requests and deliver products on time.
- Reduction in Transportation Costs: Optimized production sequencing leads to decreased transportation costs.
As demonstrated by the mentioned example, it is evident that through the implementation of MPS, a company can achieve a well-ordered and well-adjusted production process, resulting in overall production improvement and advancements in efficiency, product quality, and responsiveness to demand. This experience illustrates how the use of MPS technology can aid in enhancing performance and achieving production goals for a company.
Conclusion
Production planning, scheduling, task prioritization, and proper execution of operations are crucial aspects for the success of an industry. In fact, the backbone of a manufacturing business lies in its main production plan or the Master Production Schedule (MPS). Without proper production scheduling, the risk of producing more or fewer products than current demand exists, potentially leading to damages for the company.
Therefore, in this article, an effort was made to briefly explain the main production scheduling, the application of MPS, the objectives of MPS, the benefits of production scheduling, and more. It is hoped that the provided information has been useful and practical for you. If you have any questions or comments about this article, please don’t hesitate to get in touch with us through comments.
Leave a Reply
Want to join the discussion?Feel free to contribute!